SOPV-subsidie: Versnel jouw omschakeling naar circulaire plastics
In de komende jaren wordt naar verwachting het gebruik van gerecyclede en biogebaseerde plastics ter vervanging van fossiele grondstoffen gestimuleerd. De tijd om voor te sorteren is dus nu! Verwerk jij fossiele plastics tot (deel)producten voor de Nederlandse markt? Ontdek dan hoe je met behulp van de vernieuwde SOPV-subsidie jouw bedrijf klaarstoomt voor de toekomst.
Wat wordt er gesubsidieerd?
- Productietesten met gerecycled en/of biogebaseerd plastic.
- Inkoop van expertise of advies bijvoorbeeld materiaalkundige ondersteuning.
- Kosten van externe testen bijvoorbeeld laboratoriumproeven.
- Deskundig onderzoek bijvoorbeeld deskstudies.
- Aanpassingen aan apparatuur of matrijzen.
75% van de kosten worden vergoed, tot maximaal € 25.000 per aanvrager.
Waarom nu testen?
Met productietesten ontdek je hoe circulaire plastics invloed hebben op je proces en productkwaliteit. Denk aan aspecten zoals:
- Treksterkte en impactweerstand
- Verwerkbaarheid (vloeigedrag, geur, kleur en krimp)
- Noodzakelijke aanpassingen in machine-instellingen
Door nu te testen, verklein je de risico’s, optimaliseer je je proces en voldoe je straks volledig aan de nieuwe eisen.
Zo pak je een productietest aan
- Voorbereiding: Selecteer geschikte circulaire grondstoffen en voer basistesten uit (bijvoorbeeld mechanische eigenschappen en vervuiling).
- Labproef: Test op kleine schaal verschillende mengverhoudingen (bijvoorbeeld 15%, 30%, 50%) om proces- en productimpact te beoordelen.
- Productieschaal: Voer een proef uit op je eigen machines om praktijkresultaten te valideren.
Zelf testen of uitbesteden?
Voorkom minder verstoring van je productie door het uitbesteden van de tests. Daarnaast heb je meer controle en ontvang je een gedegen testrapport.
Hulp nodig?
Onze experts denken graag met je mee! Of je nu ondersteuning zoekt bij het opzetten van een test, behoefte hebt aan materiaalanalyse, of begeleiding wilt bij de subsidieaanvraag — wij staan klaar. Neem vrijblijvend contact met ons op of vraag direct een offerte aan om te starten.
Grijp deze kans en zet nu de stap naar circulair succes!
Meer informatie over de regeling vind je op rvo.nl/sopv.
De kunststofindustrie is een sector in ontwikkeling waarin precisie, efficiëntie en kwaliteit centraal staan. Spuitgieten is een complex proces met veel variabelen. Voor operators die dit proces beter willen begrijpen en sneller hun vaardigheden willen ontwikkelen, zijn de cursussen Spuitgieten 1 & 2 een waardevolle investering. Maar wat is precies het verschil tussen deze twee cursussen, en waarom zou een operator ze volgen?
Spuitgieten 1: De basis van het vak
De cursus Spuitgieten 1 is bedoeld voor beginnende operators of medewerkers die te maken hebben met spuitgieten en zich willen verdiepen in het spuitgietproces. Hierin komen de volgende onderwerpen aan bod:
- Functie en werking van de spuitgietmachine en matrijs
- Eigenschappen van kunststoffen en het effect op het proces
- Basisprincipes van het spuitgietproces
- Opstarten van de machine en monitoren van een proces
- Omstellen van een spuitgietmachine
- Herkennen van veelvoorkomende fouten en basisoplossingen
Met deze cursus krijgen operators een solide basis om veilig en efficiënt te werken met spuitgietmachines. Ze bouwen praktijkervaring op en leren hoe ze bestaande spuitgietprocessen kunnen controleren en eenvoudige problemen kunnen oplossen (met minder materiaalverlies en machinestoring tot gevolg).
Spuitgieten 2: Verdieping en proces opbouwen
De cursus Spuitgieten 2 is bedoeld voor operators en machinestellers die al ervaring hebben met spuitgieten en hun kennis willen uitbreiden. Tijdens deze cursus wordt er dieper ingegaan op:
- Het controleren van je apparatuur, gereedschap en grondstof
- Verdieping in de samenhang van procesvariabelen
- Opzetten en instellen van een spuitgietproces
- Instellen van bewakingen en proces monitoring
- Het oplossen van spuitgietfouten
- Eenvoudige berekeningen
Met deze cursus wordt een bredere basis voor doorgroei of meer verantwoordelijkheid gelegd. De operator krijgt kennis en hulpmiddelen om op een gestructureerde manier een spuitgietproces op te bouwen voor nieuwe matrijzen en grondstof combinaties.
Waarom zou een operator deze cursussen volgen?
- Productkwaliteit: Een operator die het spuitgietproces begrijpt kan defecten voorkomen en zorgt voor een stabiele productkwaliteit. Daarnaast zorgt een gestructureerde proces opbouw voor een zo groot mogelijk proces venster.
- Efficiënter werken: Door beter inzicht in het proces kan er met minder materiaalverlies en stilstand geproduceerd worden.
- Loopbaanontwikkeling: Operators met gespecialiseerde kennis zijn beter gemotiveerd, nemen meer verantwoordelijkheid en kunnen meedenken in verbetering.
- Kostenbesparing: Minder fouten, minder verspilling en minder stilstand zorgen voor lagere productiekosten.
Conclusie
Of de operator nu net begint in de kunststofindustrie of al jaren ervaring heeft, een cursus Spuitgieten 1 of Spuitgieten 2 is een slimme keuze. Door deze trainingen te volgen, kunnen operators niet alleen hun eigen vaardigheden verbeteren, maar dragen ze ook bij aan een efficiëntere en duurzamere productie. Investeren in kennis is investeren in de toekomst!
Meer informatie over de cursussen Spuitgieten 1 & 2 vind je op de website van Stodt. Neem vrijblijvend contact op met Peter van Barneveld als je meer wil weten over de trainingen die door en bij Polymer Science Park gegeven worden.
Kunststof is een heel normaal onderdeel geworden van onze maatschappij. Het wordt voor van alles en nog wat gebruikt. Eigenlijk net zoals vroeger lood en zink: beschikbare materialen waar je alles mee kunt doen en maken. Kunststof heeft ook veel voordelen boven andere materialen: het is licht van gewicht, gaat niet snel kapot als je het laat vallen en het kost niet veel om te maken. Ook als verpakkingsmateriaal is het heel geschikt. Maar zoals bij alles: naast voordelen zijn er ook nadelen. Kunnen we die nadelen verkleinen door het gebruik van biologisch afbreekbare kunststoffen?
Als we het gebruik van glas met kunststof in de verpakkingsindustrie vergelijken, zien we dat het nadeel van glas ten opzichte van kunststof is dat het zwaarder en kwetsbaarder is dan kunststof in het dagelijks gebruik. Daar staat als voordeel tegenover dat glas geen milieuschade oplevert (behalve als je er met je blote voeten in trapt) omdat het in de natuur in de loop van tijd wordt afgebroken. Glas wordt in op natuurlijke wijze ontbonden in zand en wat kalk. Kunststof dat in de natuur terechtkomt, wordt afgebroken tot kleinere deeltjes die wel degelijk een risico voor mens en dier vormen. Net zoals de loden voorwerpen, die bleken toch niet zonder risico te zijn: er kwam veel lood in het bloed van mensen en dat zorgde onder andere voor zenuw-gerelateerde aandoeningen.
Waarom moeten kunststoffen biologisch afbreekbaar zijn?
De meest gebruikte kunststoffen zie je in de afbeelding hieronder. Het zijn allemaal kunststoffen die niet of nauwelijks in de natuur worden afgebroken. Maar glas is ook niet biologisch afbreekbaar en toch vraagt niemand naar biologisch afbreekbaar glas. Het kan honderden jaren duren voordat glas in de natuur geheel is ontbonden: beter gezegd: kapot is gegaan. Waarom zou kunststof dan wel biologisch afbreekbaar moeten zijn? Nou, dat komt omdat kunststoffen in het milieu na enige tijd ‘slijten’ maar niet ontbinden.
Als kunststoffen in het milieu terechtkomen, worden ze kleiner en kleiner en tenslotte spreken we van micro- of nano-plastics. Microplastics zijn allerlei vormen van plastics (bolletjes, fragmenten, vezels, schuim) zoals polyetheen, die kleiner zijn dan 5 mm. Nanoplastics zijn van hetzelfde materiaal en vorm maar zijn kleiner dan 1 micrometer. En dat is precies het probleem. De afbraakproductenzijn in dezelfde grootteorde als onze lichaamscellen: immuun cellen (6 – 80 micrometer) en andere cellen in ons lichaam. Daardoor worden ze makkelijk opgenomen in ons lichaam, maar ook in het lichaam van vissen en dieren. Als je bijvoorbeeld kippen laat scharrelen op een stuk grond waar ook plastic is terechtgekomen, komen microplastics in het lichaam van een kip terecht. En wij eten die kip dan weer. Maar ook schelpdieren, vissen en veel andere organismen nemen deze plastics op en die hebben dan effect op hun leven. Plastics kunnen ontstekingsreacties veroorzaken omdat ze reageren met witte bloedcellen. Maar er zijn veel meer effecten bekend van kunststoffen op ons lichaam, zoals hieronder te zien is.
Weekmakers
De weekmakers die gebruikt worden bij plastics hebben in het lichaam een effect dat lijkt op dat van het hormoon oestrogeen: ze worden dan ook xeno-oestrogenen genoemd. Daarnaast vormen weekmakers zoals Bis-Phenol-A (BPA) een risico voor het ongeboren kind. Dus niet alleen de kunststoffen zijn schadelijk, maar ook de stoffen die worden gebruikt om de kunststoffen flexibel te maken zijn schadelijk. Deze stoffen komen vrij bij de afbraak van kunststof in het milieu.
Twee wegen om kunststoffen biologisch af te breken
De meeste kunststoffen zijn polymeren met weinig tot geen functionele groepen die aantrekkelijk zijn voor micro-organismen (bacteria, schimmels, protozoa en sommige algen). Om kunststoffen toch biologisch afbreekbaar te maken, kijken we naar twee manieren.
Meer functionele groepen
De ene manier om biologisch afbreekbare kunststoffen te maken is meer functionele groepen inbouwen in het polymeer. Bijvoorbeeld polymelkzuur is een soort kunststof die beter afbreekbaar is dan de gebruikelijke kunststoffen. Andere kunststoffen die biologisch afbreekbaar zijn, zijn onder andere:
- Polybutyleen
- Polyhydroxyalkanoaat
- polybutyleen succinaat
- polybutyleentereftalaat
- polycaprolacton
Maar deze kunststoffen hebben weer andere eigenschappen dan de gebruikelijke kunststoffen zoals PET en PVC. Bovendien is de productie van polymelkzuur en de andere biologisch afbreekbare kunststoffen op dit moment duurder.
Micro-organismen
De andere manier is om micro-organismen te selecteren die beter kunnen omgaan met deze polymeren. Bacteria hebben de eigenschap dat ze snel kunnen muteren. Soms is dat hinderlijk (denk aan bacteria die ongevoelig worden voor antibiotica), maar soms is dat een voordeel. Als je veel bacteria als in een microfilm op een petfles laat zitten, zullen er uiteindelijk een paar bacteria zijn die een enzym ontwikkelen dat die petfles kan afbreken.
Een sprookje? Nee. In 2016 werd een bacterie ontdekt in een slijmlaag op een petfles die PET-ase als enzym had ontwikkeld. Dit enzym (die je hiernaast ziet) kan petflessen vervolgens langzaam afbreken. Maar ook deze ontwikkeling staat nog in de beginfase en moet de komende tijd worden uitgebreid. Zoals het vinden van meer micro-organismen (of maken met genetisch modificatie) met enzymen die de huidige kunststoffen kunnen afbreken en optimaliseren van de afbraak. Een belangrijk nadeel is dat er op dit moment meer kunststof in het milieu komen dan de micro-organismen aankunnen. De bacteria moeten nog even wennen aan deze nieuwe stoffen, dus de boodschap blijft: gooi geen kunststof weg in het milieu.
Deze blog is tot stand gekomen in samenwerking met de Chemische Kring Zwolle en geschreven door Guillaume Counotte.
Hoe nu verder?
Bij Polymer Science Park zijn we volop bezig met de ontwikkeling en het testen van biopolymeren. Ook jij kan hierbij aansluiten. Voor meer informatie kun je contact opnemen met Erwin Zant, projectleider bij PSP.
Bronnen:
Figuur 2: Nurshad Ali, Jenny Katsouli, Emma L. Marczylo, Timothy W. Gant, Stephanie Wright, Jorge Bernardino de la Serna, The potential impacts of
micro-and-nano plastics on various organ systems in humans, eBioMedicine, Volume 99, 2024, 104901, ISSN 2352-3964,
Figuur 3: PALM, Gottfried J., et al. Structure of the plastic-degrading Ideonella sakaiensis MHETase bound to a substrate. Nature communications, 2019, 10.1: 1717.
Heb je ooit geprobeerd om recyclaat te gebruiken, maar produceerde je vooral afgekeurde producten? Kan het zijn dat recyclaat met dezelfde MFI (Melt Flow Index) toch anders vloeit tijdens verwerking dan virgin kunststof? In dit kennisblog gaan we in op de oorzaken van afwijkend vloeigedrag van recyclaat, hoe je dit kunt meten en, belangrijker nog, wat je kan doen tijdens verwerking.
Het vloeigedrag van recyclaat kan een grote uitdaging vormen in productieprocessen zoals spuitgieten en extruderen. Waar virgin kunststoffen een consistent en voorspelbaar vloeigedrag vertonen, kan dit bij recyclaat variëren en voor verrassingen zorgen.
Oorzaken van afwijkend vloeigedrag bij recyclaat
De belangrijkste oorzaak van afwijkend vloeigedrag bij recyclaat, is de vervuiling van andere grades. Neem bijvoorbeeld High Density Polyethyleen (HDPE). Een HDPE grade die ontwikkeld is voor een shampoofles, heeft andere vloei-eigenschappen dan een HDPE gebruikt voor een krat. Polymeer ketens in virgin kunststoffen zijn meestal mooi gelijkmatig verdeeld in lengte. Bij recyclaat kunnen deze ketens onregelmatiger zijn, omdat er verschillende bronnen (grades) gemengd met elkaar zijn. Daarnaast zijn de ketens van recyclaat gemiddeld gezien iets korter, omdat ze tijdens het recyclingproces af kunnen afbreken. Ook dit zorgt ervoor dat recyclaat zich anders gedraagt dan virgin, de ketenlengte heeft namelijk invloed op het vloeigedrag.
Afwijkende vloei herkennen
Afwijkingen in vloeigedrag kunnen bij het produceren met recyclaat tot de volgende uitdagingen leiden:
1. Wisselende matrijsvulling
De hoeveelheid materiaal die in de mal gespoten wordt (het shotvolume) kan wisselen wanneer het vloeigedrag fluctueert. Hierdoor kunnen producten soms ongevuld of juist overvol (risico vliesvorming) zijn.
2. Verschil in druk
Wisselend vloeigedrag kan leiden tot een verhoging of verlaging van je druk in het spuitgietproces.
Door het herkennen van een afwijkende viscositeit ten opzichte van virgin, kan je tijdens het proces bij proberen te sturen. Een aantal parameters waarmee bijgesteld kan worden zijn inspuitsnelheid, shotvolume of verwerkingstemperatuur. Bedrijven die hun procesvenster duidelijk hebben, weten hoe veel ze kunnen bijsturen met deze parameters tijdens het proces.
Voorkomen van problemen; meet vloeigedrag!
Problemen in productie veroorzaakt door vloeigedrag kan je het beste voorkomen door vooraf het materiaal te analyseren. Daarvoor zijn verschillende methoden beschikbaar. We hebben de meest gebruikte technieken voor je op een rij gezet en het meetbereik in de onderstaande grafiek verwerkt:
MFI (Melt Flow Index)
De MFI staat toch al in de datasheet? Dat klopt. MFI is de meest voorkomende opgegeven indicatie van je vloeigedrag. Wanneer er op een datasheet een bereik weergegeven is, kan het waardevol zijn dit na te meten. Bij deze meting wordt er onder een verhoogde temperatuur een gewicht, (voorgeschreven in ISO-normen) op het materiaal gedrukt. Er wordt vervolgens gewogen hoeveel materiaal er in 10 minuten uit vloeit. Omdat dit bij lage afschuifspanning (zie kader) is, kan het zijn dat een recyclaat dezelfde MFI heeft, maar zich toch nog anders gedraagt in productie, onder hoge afschuifspanning.
Voordeel:
- Deze test geeft in de basis een snelle indicatie van de viscositeit.
Nadelen:
- Deze test houdt geen rekening met de hoge afschuifsnelheden in productie.
- Het geeft slechts een indicatie van het vloeigedrag onder specifieke omstandigheden.
Capillaire reometrie
Deze geavanceerde methode wordt uitgevoerd op een speciale reometer. Het monstermateriaal wordt in een verwarmde cilinder gebracht waarin met een plunjer verschillende snelheden worden aangebracht. Afhankelijk daarvan meet je de druk en daarmee de viscositeit bij wisselende afschuifsnelheden. Hierdoor krijg je een volledige viscositeitscurve, een voorbeeld daarvan vind je hieronder. Je kunt dit op meerdere temperaturen herhalen.
Voordelen:
- Deze test meet de viscositeit bij verschillende afschuifsnelheden en temperaturen
- Ideaal als je weinig testmateriaal beschikbaar hebt
- Geeft een volledige viscositeitscurve
Nadeel:
De test wordt uitgevoerd op een testapparaat en is redelijk bewerkelijk en duur vergelijken met MFI. Tevens moet je de uitkomsten kunnen interpreteren. Je krijgt met de uitkomsten nog geen inzichten waarmee je je machines goed in kan stellen.
Spiral flow
Dit is vergelijkbaar met de capillaire reometrie. Deze techniek voer je uit op een spuitgietmachine. Met deze techniek spuit je het monstermateriaal, met verschillende inspuitsnelheden, in een spiraalmatrijs. Vervolgens meet je hoe ver de spiraalmatrijs gevuld is. Hoe beter het materiaal vloeit, des te verder zal de spiraal gevuld zijn. Zo kun je verschillende materialen met elkaar vergelijken.
Overige voordelen:
- Vergelijkt materialen onder praktijkomstandigheden
- Meet de vloeilengte in relatie tot de in spuitsnelheid
- Simuleert het werkelijke productieproces
Nadeel:
Relatief kostbaar, tijdsintensief en je moet de machine ombouwen na de test om weer normale producten te maken.
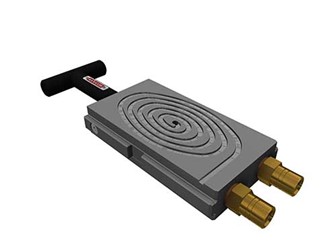
Spiral Flow matrijs. Bron: Axxicon
Viscositeitsproef PSP
Deze methode combineert elementen van capillaire reologie en spiral flow.Net als bij de spiral flow, varieer je de inspuitsnelheid. Je meet echter niet hoeveelheid materiaal die er uitkomt, maar de druk. Hiermee krijg je een relatieve viscositeitscurve, vergelijkbaar met capillaire rheologie. Omdat je dit op je eigen machines en matrijs kunt uitvoeren, kun je de gemeten parameters meteen toepassen in productie.
Voordelen:
- Uitgevoerd op je eigen machines
- Meet relatieve viscositeit in verhouding tot je specifieke machine, matrijs en instellingen
- Toont bij welke inspuitsnelheid en druk de viscositeit stabiel is
- Geen ombouw van de machine nodig na de test
Nadelen:
- Kan meer tijd en materiaal kosten
- Resultaten zijn matrijs en machine afhankelijk, je meet niet de absolute afschuifsnelheid en viscositeit, maar een relatieve waarde
Ons advies
Door deze verschillende methoden te combineren, krijg je een compleet beeld van het vloeigedrag van recyclaat. Begin met een MFI-test voor een snelle indicatie of selectie van materiaal. Vervolgens is het aan te raden om vloeigedrag van recyclaat en virgin te vergelijken met diepgaandere analyse methode.
Stel je machines zorgvuldig in
Recyclaat kan wisselend vloeigedrag vertonen, wat betekent dat je misschien het shotvolume en de inspuitsnelheid moet aanpassen om te voorkomen dat producten halfgevuld of overvol raken. Het is belangrijk om te weten bij welke instellingen de vloei stabiel en betrouwbaar blijft. Gebruik daarom de resultaten uit de eerdere proeven (als de viscositeitsproef) om je machines optimaal in te stellen.
Train je productieteam
Zelfs met de juiste materiaalkeuze en machine-instellingen kunnen er tijdens de productie nog verschillen in vloeigedrag ontstaan. Door je operators goed op te leiden kunnen ze het proces bij sturen op de eerder genoemde parameters.
Ervaar je nog steeds problemen?
Als je na deze stappen nog steeds problemen ondervindt, dan kun je overwegen om samen met recyclers het vloeigedrag aan te passen. Bijvoorbeeld door het toevoegen van peroxiden tijdens het extruderen of door recyclaat te mengen met virgin materiaal. Hierover meer in ons volgende blog.
Nu je de oorzaak van het afwijkende gedrag kent, weet welke meetmethoden toe kunt passen én de oplossingen kent, heb je alle handvatten om recyclaat succesvol te integreren in je product. Veel succes!
Meer weten
Heb je vragen over het vloeigedrag van recyclaat of wil je advies over de beste aanpak voor jouw product en proces? Neem dan contact met ons op, we helpen je graag verder.
Werk je al met kunststof recyclaat of wil je hiermee starten? Dan is het belangrijk dat je er rekening mee houdt dat dit materiaal verontreinigd kan zijn. Hoe dit komt, wat het voor jouw product betekent én hoe je dat kan meten leggen we je uit in dit artikel. Ook hebben we een helder plan van aanpak voor je uitgeschreven, zodat je precies weet waar je moet beginnen.
Van afval tot kunststof recyclaat
Recyclaat wordt gemaakt uit afvalstromen. Tijdens het gebruik, de inzameling en in het recyclingproces is het materiaal dan ook met allerlei verontreinigde stoffen en materialen in aanraking geweest. Om zoveel mogelijk vuil te verwijderen, passen recyclers verschillende scheidingstechnieken toe. Deze variëren van handmatige scheiding tot geavanceerde methoden zoals kunstmatige intelligentie (AI), zink-drijf (waterbad), infraroodscanners en elektrostatische scheiding. Om de laatste vuilresten – met name inkten en lijmen van etiketten – te verwijderen worden de materialen ook nog gewassen. Dit is een belangrijke stap en is volop in ontwikkeling. Denk bijvoorbeeld aan van koud naar warm tot frictie wassen.
Productieproblemen door verontreinigd recyclaat
Ondanks dit scheidings- en wasproces, blijft er regelmatig vuil in het recyclaat achter. Op het oog is dit niet waarneembaar. Maar als je verontreinigd recyclaat gebruikt, dan kun je in productie of tijdens de productlevensduur tegen allerlei problemen aanlopen. Denk aan een verminderde sterkte van het product, doordat de vervuiling lokaal voor een zwakke plek zorgt.Op de afbeelding hiernaast is bijvoorbeeld een breuk ontstaan door aanwezigheid van PET-vervuiling in een Polypropyleen product. Maar ook aan verkleefde en verstopte matrijzen. Daarnaast kun je oneffenheden of verkleuringen in je product ontdekken.
Het is dus erg belangrijk om van tevoren te weten of het recyclaat dat je gekocht hebt verontreinigd is. Misschien ervaar je al problemen en vraag je je af waar dit door komt. Ook in dat geval is een analyse van het recyclaat een goede stap om te ontdekken of de oorzaak bij verontreiniging ligt.
Soorten verontreiniging van gerecycled kunststof
Er zijn verschillende methodes om recyclaat te analyseren op verontreiniging. Deze leggen we hieronder uit. Welke analysemethode je het beste toe kunt passen hangt af van het type verontreiniging dat je verwacht aan te treffen. Er zijn drie soorten:
- Polymeerverontreiniging: denk aan Polyethyleen (PE) vervuild met kleine hoeveelheden Polyproplyleen(PP), afkomstig uit doppen, sluitingen of andere producten. Er kunnen bijvoorbeeld ook nog inkten en lijmresten in het recyclaat aanwezig zijn.
- Verontreiniging door vocht en vluchtige organische stoffen (VOC).
- Anorganische verontreiniging, zoals zand, klei, stof, metaal en vulstoffen.
Polymeerverontreiniging onderzoeken
Heb je het vermoeden dat er sprake is van polymeerverontreiniging? Dan kun je de DSC– (op basis van verhitting/koeling) en/of de FTIR-analyse (op basis van Infrarood) toepassen. Met FTIR-analyses worden met behulp van een infraroodscanner specifieke functionele groepen achterhaald – door middel van een uniek piekenpatroon – om het materiaaltype te identificeren. De focus ligt bij deze analyse op de verbindingen tussen de moleculen.
Bij sommige polymeren, zit er overlap in het piekenpatroon en is het met FTIR-analyse lastig te zien welke polymeren verontreinigd zijn. Dan kun je de meting aanvullen met een DSC-analyse. Bij DSC wordt er onder andere gekeken naar de smelttemperatuur, kristallisatietemperatuur en de Glas Transitie Temperatuur (Tg). Deze testmethode kan ingezet worden om het (hoofd) materiaaltype te identificeren, maar ook de verontreiniging van andere polymeren aan de hand van hun Tg of smelt punt te detecteren.
Tip: om een volledig beeld van polymeerverontreiniging te krijgen raden wij aan om beide analyses uit te voeren.
Verontreiniging door anorganische stoffen, vocht, VOC’s en vulstoffen uitsluiten
Vermoed je dat er vocht en anorganische stoffen in het materiaal zitten? Of dat er VOC’s vrijgekomen zijn tijdens het productieproces? Dan kun je dit op twee manieren achterhalen.
- TGA-test
Je kunt een sample thermografisch (laten) analyseren, afgekort TGA. Bij deze meting wordt het recyclaat verhit tot 800 °C. Tijdens dit verhittingsproces wordt de gewichtsafname gemeten. Zo kan er worden bepaald of er vocht of VOC’s vrijkomen en bij welke temperatuur de kunststof sterk in gewicht afneemt en dus degradeert. In de asrest van deze test vind je de anorganische stoffen terug. Hierbij kun je denken aan glasvezels, zand en vulststoffen zoals krijt en mineralen. - Verassingstest
Als je alleen de asrest wilt bepalen kun je ook een (simpelere) verassingstest uitvoeren. Bij deze test verhit je een sample tot 600 °C en meet je het gewicht voor en na de verassing.
Verbredende analyse
Wil je de asrest (de anorganische verontreiniging) uit de TGA of de verassingstest nog verder analyseren? Dan kan dat met behulp van een optische microscoop. Hiermee ontdek je hoe groot en welke vorm de deeltjes hebben. Zo kun je veel te weten komen over de bron van de verontreiniging.

Microscopische foto vervuiling in dunwandig product, gemaakt van recyclaat
Gespecialiseerde analyses voor extra verdieping
Om nog beter te bepalen met welke verontreiniging je te maken hebt, kun je een geavanceerde SEM-EDX microscoop inzetten. Hiermee bepaal je uit welke atomen de verontreiniging bestaat. Denk bijvoorbeeld aan aluminium of calcium door verschillende vulstoffen.
Als je met de TGA-analyse een hoge concentratie van VOC’s hebt waargenomen, dan kun je met behulp van chromatografie (GC/MS) analyseren welke dit zijn. Er zijn zelfs methodes die het gebruik van bijvoorbeeld UV-absorbers of andere additieven in hele lage concentraties in kunststoffen kunnen detecteren. Daarnaast kun je ook in de praktijk verontreiniging testen. Bijvoorbeeld door het filter residu (een stof die overblijft na een proces) na je extrusie verder te analyseren. Deze gespecialiseerde methodes gebruik je alleen wanneer het nodig is om de diepte in te gaan.
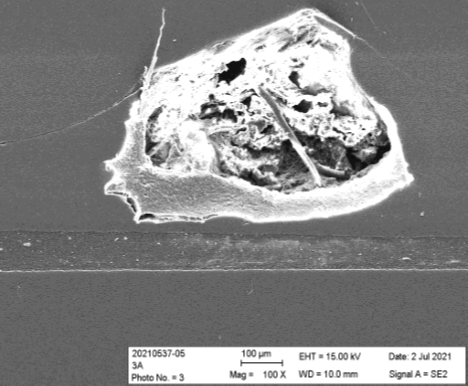
SEM-EDX zoom van dezelfde vervuiling in dunwandig product, gemaakt van recyclaat. Met SEM EDX is de samenstelling van deze vervuiling bepaald en kon de bron worden achterhaald.
Plan van aanpak
Verontreinigd recyclaat kan dus tot problemen leiden. Wil je dit oplossen of wil je meer weten dan alleen de specificaties van de leverancier? Dan stellen we onderstaand plan van aanpak voor:
.
Analyses gesubsidieerd (laten) uitvoeren
Om het gebruik van recyclaat te stimuleren, heeft het Ministerie van Infrastructuur en Waterstaat de ‘Tijdelijke subsidieregeling omschakeling naar verwerking circulaire plastics’ ter beschikking gesteld. Met deze subsidie krijg je 75% van de onderzoekskosten vergoed voor het uit (laten) voeren van productietesten en verbonden activiteiten, waaronder het selecteren en analyseren van het beoogde recyclaat. Er is per bedrijf tot € 25.000,- subsidie beschikbaar! De aanvraag is op 18 juni jl. geopend en loopt tot 3 oktober 2024. Op is op, dus stuur nog snel jouw aanvraag in. Lees meer over deze subsidie.
Hulp nodig?
We denken graag met je mee over welk type verontreiniging er zou kunnen spelen en welke test- en analysemethode daar het beste bij aansluit. Naar wens kunnen we je ook bij het uitvoeren van de analyses en productietests ondersteunen. Neem daarvoor vrijblijvend contact met ons op.
Operators weten precies op welke knoppen ze moeten drukken. Dat ‘trucje’ doen zij natuurlijk dagelijks. Maar wat als er problemen ontstaan? Weten zij dan ook precies wat er aan de achterkant gebeurt? En hoe ze dit adequaat oplossen om productuitval te voorkomen?
Betrokkenheid tonen en verantwoordelijkheid nemen van het productieproces zijn belangrijke redenen waarom bedrijven in de kunststofbranche investeren in het opleiden en doorontwikkelen van hun personeel. Zij willen dat het personeel zich verantwoordelijk voelt voor ‘hun’ proces en kleine storingen zelf op kunnen lossen.
In deze blog ontdek je welke opleidingssoorten er in de kunststofbranche zijn en wat de voor- en nadelen hiervan zijn. En onderaan vind je vier kernvragen waarmee je een weloverwogen keuze maakt.
De vier type opleidingen en trainingen in de kunststofbranche
Het landschap voor opleidingen, cursussen en trainingen over (het werken met) kunststoffen is breed. Waar moet je als bedrijf in de kunststof sector voor kiezen? Om je een handje te helpen hebben wij de vier verschillende opleidingsmogelijkheden voor je op een rij gezet. Bekijk ze ook in de tabel verderop in deze blog.
-
HBO-opleidingen
In Nederland zijn er meerdere HBO-instellingen die opleidingen voor de kunststofbranche aanbieden op zowel bachelor als master niveau. Zoals de opleiding Polymer Engineering of Polymer Design Engineering. Deze opleidingen zijn vaak tweejarig (bestaande uit meerdere modules).
- Medewerkers gaan echt de diepte in en ontvangen na een succesvolle afronding een erkend HBO-diploma.
- Houd er rekening mee dat dit type opleiding een aardige investering is, zowel in tijd (2 jaar lang een dag in de week) als geld (gemiddeld 11.250 euro per jaar).
-
MBO-opleidingen
In tegenstelling tot de HBO-opleidingen, duren de MBO-(deel)opleidingen gericht op kunststof vaak slechts enkele lesdagen. Zo ronden medewerkers de opleiding Kunststoftechniek van het Deltion College al binnen 10 lesdagen (20 dagdelen in 10 weken) af.
- Dit zijn relatief korte opleidingen, die medewerkers met een (niveau 4) MBO-certificaat afsluiten.
- Deze opleidingen zijn breed en geven een goede basis. Net als de HBO-opleidingen vinden deze opleidingen niet plaats op locatie.
-
Praktijktrainingen
Praktijktrainingen, van bijvoorbeeld een opleider als STODT, gaan in op een specifiek onderdeel van het kunststofproductieproces. Denk bijvoorbeeld aan spuitgieten 1,2 of 3 of extruderen 1. Deze cursussen worden bij voldoende resultaat afgesloten met een landelijk branche-erkend diploma (VAPRO).
- Goede basistrainingen specifiek op verwerkingstechniek die als start dienen voor verdere doorontwikkeling.
- De opleidingen zijn vaak breed en (de theorie) niet helemaal toegespitst op de materialen, machines en het proces van de opdrachtgever.
-
Maatwerk kunststof trainingen (op locatie)
Bij dit opleidingstype wordt er vaak voorafgaand aan de training een intake van een halve dag gedaan, om de wensen en het kennisniveau van de groep in kaart te brengen. Zo kan er tijdens de training specifiek ingegaan worden op bepaalde materialen (bijvoorbeeld PVC, PET, PA, regrinds en recyclaat), verwerkingstechnieken (bijvoorbeeld spuitgieten, extruderen en blaasextrusie) en handelingen en komen er geen ‘onnodige onderwerpen’ aan bod. De training wordt op de productielocatie gegeven door een vakspecialist, in samenwerking met jullie eigen specialisten. Ook wordt er op jullie eigen machines en met jullie eigen materialen worden gewerkt. Maatwerk trainingen kunnen georganiseerd worden voor diverse afdelingen; operations, research & development, maar ook de niet-technische (bijvoorbeeld verkoop) afdelingen.
- Dit is een kortdurende training, die op jouw eigen locatie plaatsvindt en waarbij gebruik van jullie eigen materialen en machines gemaakt wordt. Hierdoor kan de opgedane kennis vaak direct toegepast worden.
- De medewerkers doen de benodigde vakkennis gericht op, maar ontvangen geen certificaat of diploma.
Een keuze maken? Stel jezelf deze 4 kernvragen
Op basis van de opleidingstypes hierboven, zijn dit de vier kernvragen die je jezelf kunt stellen om een weloverwogen keuze voor jouw personeel te maken.
- Is het belangrijk dat de medewerkers een erkend diploma of certificaat ontvangen?
Bij een HBO-, MBO- en een praktijktraining ontvangen medewerkers na een succesvolle afronding een erkend diploma, (deel)certificaat of VAPRO certificaat. Bij maatwerk trainingen is dit niet het geval.
- Is het van belang dat de training op locatie gegeven wordt en er gebruikgemaakt wordt van de eigen machines en materialen?
Een training op de eigen werkplek van de medewerker heeft grote voordelen voor het leereffect. Hij of zij leert alle ins-en-outs van zijn eigen machines kennen en de materialen die hij of zij dagelijks gebruikt. Vind je dit belangrijk? Dan is een praktijktraining op locatie of een maatwerktraining interessant voor jou.
- Hebben de medewerkers al basiskennis (bijvoorbeeld spuitgieten 1) en zijn ze juist op zoek naar verdieping?
Afhankelijk van het kennisniveau van je medewerkers kun je dan kiezen voor vervolgtraining bij een praktijkopleider, zoals spuitgieten 2 of 3. Dit is een vast programma, dat onderwerpen kan behandelen die medewerkers al beheersen. Het alternatief is een maatwerktraining (op locatie). Deze trainingen zijn aan te passen naar het kennisniveau van de medewerkers (van beginner tot expert) en zijn specifiek af te stemmen op de leerbehoefte. In tegenstelling tot een vervolgtraining bij een praktijkopleider, volgen medewerkers bij een maatwerk training geen volledige modules. Ze zoomen in een maatwerk training naar wens in op de onderwerpen waar zij tegenaan lopen of meer over willen leren.
- Welk opleidingsbudget is er beschikbaar?
Er zitten veel verschil in prijs en opleidingsduur van de verschillende opleidingstypes. Om je een beeld van deze verschillen te geven, hebben we (op 26-04-2024) een greep genomen uit de opleidingsprijzen en duur en deze voor je op een rij gezet in de onderstaande tabel.
.
Van trucje naar vakmanschap
Eén ding is zeker: welke training, opleiding of cursus over kunststof je ook kiest, hiermee geef je jouw personeel de benodigde handvatten om de stap te maken van het uitvoeren van een trucje naar écht vakmanschap.
Ben je op zoek naar een kunststof opleiding voor jouw personeel? Wij adviseren je graag over een kunststof opleiding die past bij jouw wensen en die van je personeel. Neem daarvoor vrijblijvend contact op met Peter van Barneveld, Business Manager Training.