Ferr-Tech versterkt ons netwerk met groene innovatie
Polymer Science Park (PSP) verwelkomt Ferr-Tech als nieuwste deelnemer binnen het netwerk. Dit vooruitstrevende bedrijf uit de chemische sector, werd nummer 1 in de KVK Innovatie Top 100 met hun gepatenteerde product FerSol®. Dit product biedt duurzame oplossingen voor afvalwaterbehandeling en kunststofrecycling. In een interview met Judith le Fèvre, mede-eigenaar en verantwoordelijk voor strategie, marketing en PR, deelt zij de visie en toegevoegde waarde van de samenwerking met PSP.
Innovatie in waterbehandeling en kunststofrecycling
Ferraat(VI) staat al decennia wereldwijd bekend als de sterkste oxidant voor waterbehandeling van afvalwater.
Tot op heden was het niet mogelijk om Ferraat(VI) stabiel en houdbaar te produceren. Ferr-Tech heeft in zeven jaar onderzoek een doorbraak gerealiseerd in het houdbaar en stabiel produceren van Ferraat(VI), een krachtige en milieuvriendelijke oxidant.
“Met ons gepatenteerde productieproces kunnen we nu FerSol® in grote volumes leveren, stabiel en houdbaar voor industriële toepassingen.”
aldus Le Fèvre.
FerSol® biedt unieke voordelen voor de kunststofrecyclingmarkt. Het product maakt het mogelijk om plastic flakes te wassen bij kamertemperatuur in plaats van bij 85 graden Celsius. En door de kracht van FerSol® bereik je dezelfde resultaten in het was proces met veel minder chemie. Daarnaast is het ook nog een groen milieuvriendelijk product. Dit verlaagt niet alleen de energiekosten, maar vermindert ook het gebruik van schadelijke chemicaliën. “Hiermee leveren we een belangrijke bijdrage aan het verduurzamen van recycling.” legt Le Fèvre uit.
Samenwerking met Polymer Science Park
Het eerste contact met PSP ontstond tijdens de Plastics Recycling Show Europe (PRSE) in Amsterdam. “We zagen direct de synergie tussen onze kennis en de projecten van PSP,” vertelt Le Fèvre. “Met name de focus op wasprocessen en geurverwijdering in kunststofrecycling sluit perfect aan bij onze expertise.”
PSP speelt een cruciale rol in het verbinden van bedrijven, kennisinstellingen en innovatieprojecten binnen de polymerensector. De toetreding van Ferr-Tech versterkt dit netwerk met geavanceerde kennis op het gebied van groene chemie en duurzame processen. Het bedrijf ziet kansen om andere deelnemers te ondersteunen met oplossingen voor het verminderen van geur en het efficiënter en duurzamer maken van recyclingprocessen.
Toekomstige projecten en toegevoegde waarde
Door de samenwerking met PSP hoopt Ferr-Tech actief bij te dragen aan nieuwe projecten die gericht zijn op de verduurzaming van de kunststofketen.
“De combinatie van ons product met het kennisnetwerk van PSP biedt enorme kansen om innovatie te versnellen en echte impact te maken in duurzame industrieën.”
besluit Le Fèvre.
Wil je meer weten over deze mooie nieuwe samenwerking of de mogelijkheden binnen het netwerk van PSP? Neem dan vrijblijvend contact met ons op.
Heb je ooit geprobeerd om recyclaat te gebruiken, maar produceerde je vooral afgekeurde producten? Kan het zijn dat recyclaat met dezelfde MFI (Melt Flow Index) toch anders vloeit tijdens verwerking dan virgin kunststof? In dit kennisblog gaan we in op de oorzaken van afwijkend vloeigedrag van recyclaat, hoe je dit kunt meten en, belangrijker nog, wat je kan doen tijdens verwerking.
Het vloeigedrag van recyclaat kan een grote uitdaging vormen in productieprocessen zoals spuitgieten en extruderen. Waar virgin kunststoffen een consistent en voorspelbaar vloeigedrag vertonen, kan dit bij recyclaat variëren en voor verrassingen zorgen.
Oorzaken van afwijkend vloeigedrag bij recyclaat
De belangrijkste oorzaak van afwijkend vloeigedrag bij recyclaat, is de vervuiling van andere grades. Neem bijvoorbeeld High Density Polyethyleen (HDPE). Een HDPE grade die ontwikkeld is voor een shampoofles, heeft andere vloei-eigenschappen dan een HDPE gebruikt voor een krat. Polymeer ketens in virgin kunststoffen zijn meestal mooi gelijkmatig verdeeld in lengte. Bij recyclaat kunnen deze ketens onregelmatiger zijn, omdat er verschillende bronnen (grades) gemengd met elkaar zijn. Daarnaast zijn de ketens van recyclaat gemiddeld gezien iets korter, omdat ze tijdens het recyclingproces af kunnen afbreken. Ook dit zorgt ervoor dat recyclaat zich anders gedraagt dan virgin, de ketenlengte heeft namelijk invloed op het vloeigedrag.
Afwijkende vloei herkennen
Afwijkingen in vloeigedrag kunnen bij het produceren met recyclaat tot de volgende uitdagingen leiden:
1. Wisselende matrijsvulling
De hoeveelheid materiaal die in de mal gespoten wordt (het shotvolume) kan wisselen wanneer het vloeigedrag fluctueert. Hierdoor kunnen producten soms ongevuld of juist overvol (risico vliesvorming) zijn.
2. Verschil in druk
Wisselend vloeigedrag kan leiden tot een verhoging of verlaging van je druk in het spuitgietproces.
Door het herkennen van een afwijkende viscositeit ten opzichte van virgin, kan je tijdens het proces bij proberen te sturen. Een aantal parameters waarmee bijgesteld kan worden zijn inspuitsnelheid, shotvolume of verwerkingstemperatuur. Bedrijven die hun procesvenster duidelijk hebben, weten hoe veel ze kunnen bijsturen met deze parameters tijdens het proces.
Voorkomen van problemen; meet vloeigedrag!
Problemen in productie veroorzaakt door vloeigedrag kan je het beste voorkomen door vooraf het materiaal te analyseren. Daarvoor zijn verschillende methoden beschikbaar. We hebben de meest gebruikte technieken voor je op een rij gezet en het meetbereik in de onderstaande grafiek verwerkt:
MFI (Melt Flow Index)
De MFI staat toch al in de datasheet? Dat klopt. MFI is de meest voorkomende opgegeven indicatie van je vloeigedrag. Wanneer er op een datasheet een bereik weergegeven is, kan het waardevol zijn dit na te meten. Bij deze meting wordt er onder een verhoogde temperatuur een gewicht, (voorgeschreven in ISO-normen) op het materiaal gedrukt. Er wordt vervolgens gewogen hoeveel materiaal er in 10 minuten uit vloeit. Omdat dit bij lage afschuifspanning (zie kader) is, kan het zijn dat een recyclaat dezelfde MFI heeft, maar zich toch nog anders gedraagt in productie, onder hoge afschuifspanning.
Voordeel:
- Deze test geeft in de basis een snelle indicatie van de viscositeit.
Nadelen:
- Deze test houdt geen rekening met de hoge afschuifsnelheden in productie.
- Het geeft slechts een indicatie van het vloeigedrag onder specifieke omstandigheden.
Capillaire reometrie
Deze geavanceerde methode wordt uitgevoerd op een speciale reometer. Het monstermateriaal wordt in een verwarmde cilinder gebracht waarin met een plunjer verschillende snelheden worden aangebracht. Afhankelijk daarvan meet je de druk en daarmee de viscositeit bij wisselende afschuifsnelheden. Hierdoor krijg je een volledige viscositeitscurve, een voorbeeld daarvan vind je hieronder. Je kunt dit op meerdere temperaturen herhalen.
Voordelen:
- Deze test meet de viscositeit bij verschillende afschuifsnelheden en temperaturen
- Ideaal als je weinig testmateriaal beschikbaar hebt
- Geeft een volledige viscositeitscurve
Nadeel:
De test wordt uitgevoerd op een testapparaat en is redelijk bewerkelijk en duur vergelijken met MFI. Tevens moet je de uitkomsten kunnen interpreteren. Je krijgt met de uitkomsten nog geen inzichten waarmee je je machines goed in kan stellen.
Spiral flow
Dit is vergelijkbaar met de capillaire reometrie. Deze techniek voer je uit op een spuitgietmachine. Met deze techniek spuit je het monstermateriaal, met verschillende inspuitsnelheden, in een spiraalmatrijs. Vervolgens meet je hoe ver de spiraalmatrijs gevuld is. Hoe beter het materiaal vloeit, des te verder zal de spiraal gevuld zijn. Zo kun je verschillende materialen met elkaar vergelijken.
Overige voordelen:
- Vergelijkt materialen onder praktijkomstandigheden
- Meet de vloeilengte in relatie tot de in spuitsnelheid
- Simuleert het werkelijke productieproces
Nadeel:
Relatief kostbaar, tijdsintensief en je moet de machine ombouwen na de test om weer normale producten te maken.
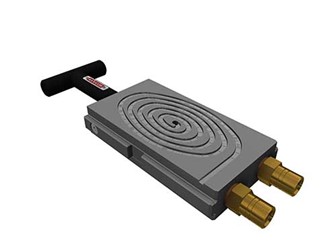
Spiral Flow matrijs. Bron: Axxicon
Viscositeitsproef PSP
Deze methode combineert elementen van capillaire reologie en spiral flow.Net als bij de spiral flow, varieer je de inspuitsnelheid. Je meet echter niet hoeveelheid materiaal die er uitkomt, maar de druk. Hiermee krijg je een relatieve viscositeitscurve, vergelijkbaar met capillaire rheologie. Omdat je dit op je eigen machines en matrijs kunt uitvoeren, kun je de gemeten parameters meteen toepassen in productie.
Voordelen:
- Uitgevoerd op je eigen machines
- Meet relatieve viscositeit in verhouding tot je specifieke machine, matrijs en instellingen
- Toont bij welke inspuitsnelheid en druk de viscositeit stabiel is
- Geen ombouw van de machine nodig na de test
Nadelen:
- Kan meer tijd en materiaal kosten
- Resultaten zijn matrijs en machine afhankelijk, je meet niet de absolute afschuifsnelheid en viscositeit, maar een relatieve waarde
Ons advies
Door deze verschillende methoden te combineren, krijg je een compleet beeld van het vloeigedrag van recyclaat. Begin met een MFI-test voor een snelle indicatie of selectie van materiaal. Vervolgens is het aan te raden om vloeigedrag van recyclaat en virgin te vergelijken met diepgaandere analyse methode.
Stel je machines zorgvuldig in
Recyclaat kan wisselend vloeigedrag vertonen, wat betekent dat je misschien het shotvolume en de inspuitsnelheid moet aanpassen om te voorkomen dat producten halfgevuld of overvol raken. Het is belangrijk om te weten bij welke instellingen de vloei stabiel en betrouwbaar blijft. Gebruik daarom de resultaten uit de eerdere proeven (als de viscositeitsproef) om je machines optimaal in te stellen.
Train je productieteam
Zelfs met de juiste materiaalkeuze en machine-instellingen kunnen er tijdens de productie nog verschillen in vloeigedrag ontstaan. Door je operators goed op te leiden kunnen ze het proces bij sturen op de eerder genoemde parameters.
Ervaar je nog steeds problemen?
Als je na deze stappen nog steeds problemen ondervindt, dan kun je overwegen om samen met recyclers het vloeigedrag aan te passen. Bijvoorbeeld door het toevoegen van peroxiden tijdens het extruderen of door recyclaat te mengen met virgin materiaal. Hierover meer in ons volgende blog.
Nu je de oorzaak van het afwijkende gedrag kent, weet welke meetmethoden toe kunt passen én de oplossingen kent, heb je alle handvatten om recyclaat succesvol te integreren in je product. Veel succes!
Meer weten
Heb je vragen over het vloeigedrag van recyclaat of wil je advies over de beste aanpak voor jouw product en proces? Neem dan contact met ons op, we helpen je graag verder.
In opdracht van ALPLA Zwolle gaf Nils Schut, Process Engineer bij Polymer Science Park (PSP), een masterclass Extrusie Blaasvormen. Met Johan van Oosten, Machine Setter bij ALPLA Zwolle, ging ik in gesprek over deze training.
Over ALPLA Nederland
ALPLA Nederland ontwerpt, ontwikkelt en produceert plastic verpakkingsoplossingen. Onder meer door middel van strekblazen en extrusieblazen. In 2020 opende ALPLA haar meest geautomatiseerde fabriek in Zwolle, voorzien van ultramoderne productietechnologieën waarmee ze voornamelijk kunststofflessen produceren. In deze fabriek werkt Johan samen met zijn collega’s aan het waarborgen van het proces en de kwaliteit van het product. Dat doen ze door het proces goed te monitoren, ondersteunen van het productieteam samen met de kwaliteitscontroles en het ombouwen van de machines op de verschillende producten. Daarnaast verzorgt Johan een deel van de opleiding van het productieteam, door middel van onder andere het maken van werkinstructies.
Trainen van (nieuwe) medewerkers
Met de groei van de fabriek, neemt het aantal nieuwe medewerkers toe. ALPLA wil ervoor zorgen dat medewerkers voldoende basiskennis hebben en de mogelijkheid krijgen voor opleiding over het product en proces. Dit leidde tot de behoefte aan een extra basistraining over verschillende kunststoffen. Naast dat de ALPLA veel kennis in huis heeft met betrekking tot de machines en het proces, hecht ALPLA waarde aan een lokale samenwerking met kunststof specialisten bij PSP. PSP beschikt als innovatiecentrum over de benodigde kennis om het personeel van ALPLA te trainen, met een focus op:
- Wat zijn kunststoffen (eigenschappen)
- Hoe verwerk je kunststoffen
- Combinaties van kunststoffen
Om een goede basistraining te ontwikkelen dat aansluit bij de dagelijkse praktijk in de fabriek, ging Nils in gesprek met Johan en Bertus Bos, Operations Manager bij ALPLA. Deze samenwerking resulteerde in de Masterclass Extrusie Blaasvormen.
Masterclass Extrusie Blaasvormen
De masterclass Extrusie Blaasvormen is een training dat bestaat uit een halve dag theorie, een halve dag praktijk bij PSP en praktijktraining op de eigen machines van ALPLA. De theorie behandelt de basiskennis over kunststoffen en het proces: wat zijn de mechanische eigenschappen van kunststoffen, hoe verwerk je ze, en wat krijg je als je ze verwerkt in een eindproduct. Vervolgens gingen de medewerkers in de praktijk aan de slag bij PSP, werkend met het materiaal van ALPLA op de spuitgietmachine om het daarna te testen in het testlab. Uniek aan de masterclass is dat Nils ook praktijktraining heeft gegeven bij ALPLA op hun eigen machines. Daardoor konden de medewerkers alle opgedane kennis gelijk toepassen in de dagelijkse praktijk.
“Ik vond het een zeer interessante training om te doen. Voor de basis is het ideaal, zeker als je zelf niet uit de kunststofwereld komt zoals ik.”
Aldus Johan van Oosten, ALPLA Zwolle
Wat heeft de masterclass opgeleverd?
De training was erg waardevol voor alle medewerkers. Het biedt een solide basis voor starters om kunststoffen te leren kennen, en voor ervaren medewerkers een opfrissing van de kennis over kunststof.
Voor medewerkers die geen achtergrond hebben in de kunststofwereld, was de theorie wel intensief. Zodoende is er voor gekozen om de masterclass op te delen in een basis training en een verdiepende training. Op deze manier sluit het goed aan bij de diverse achtergronden van de medewerkers. Met de basistraining leren starters de kunststoffen kennen, en met de gevorderde training wordt het meer toepasbaar gemaakt in de praktijk op de eigen machines. Met daarbij een hele dag praktijk bij PSP, in plaats van een middag. In de ochtend kunnen ze dan werken met de spuitgietmachine in het verwerkingslab en in de middag die kunststoffen testen in het testlab, om te zien wat bepaalde verbindingen doen met het materiaal.
“Door de praktijk ook op kleine schaal bij PSP te doen, wordt het kunststofproces veel zichtbaarder.”
Aldus Johan van Oosten, Machine Setter bij ALPLA Zwolle.
De praktijkgerichte benadering en de volledige beleving van het proces werden als grote pluspunten ervaren tijdens de training. Ook het open karakter van de training met goede interactie en ruimte voor discussie werd gewaardeerd. Dit bood een balans voor zowel theoriegeoriënteerde als praktijkgerichte medewerkers.
Wat zijn de volgende stappen voor ALPLA?
Dat er een vervolg komt op deze training is duidelijk. Nils gaat de opzet aanscherpen naar aanleiding van de evaluatie en dan is het de bedoeling dat productie personeel bij ALPLA de training gaat volgen. Het biedt een vorm van zekerheid dat iedere medewerker een basiskennis heeft van het materiaal en het proces.
“ALPLA biedt volop ontwikkelmogelijkheden voor haar medewerkers. Gezien de goede samenwerking zullen we ons ook blijven focussen op ons opleidingsaanbod vanuit PSP. Wil jij zelf een Masterclass volgen via PSP en sta jij open voor een nieuwe baan, wie weet zien we jou dan wel verschijnen in de schoolbanken bij ALPLA.”
Aldus Renate Altena-Haandrikman, HR Manager bij ALPLA Nederland.
Meer informatie
Wil je jouw medewerkers ook een vliegende start bieden in de kunststof industrie en de eigen machines beter laten begrijpen? Meer informatie over onze trainingen vind je op deze pagina, of neem vrijblijvend contact met ons op.
Werk je al met kunststof recyclaat of wil je hiermee starten? Dan is het belangrijk dat je er rekening mee houdt dat dit materiaal verontreinigd kan zijn. Hoe dit komt, wat het voor jouw product betekent én hoe je dat kan meten leggen we je uit in dit artikel. Ook hebben we een helder plan van aanpak voor je uitgeschreven, zodat je precies weet waar je moet beginnen.
Van afval tot kunststof recyclaat
Recyclaat wordt gemaakt uit afvalstromen. Tijdens het gebruik, de inzameling en in het recyclingproces is het materiaal dan ook met allerlei verontreinigde stoffen en materialen in aanraking geweest. Om zoveel mogelijk vuil te verwijderen, passen recyclers verschillende scheidingstechnieken toe. Deze variëren van handmatige scheiding tot geavanceerde methoden zoals kunstmatige intelligentie (AI), zink-drijf (waterbad), infraroodscanners en elektrostatische scheiding. Om de laatste vuilresten – met name inkten en lijmen van etiketten – te verwijderen worden de materialen ook nog gewassen. Dit is een belangrijke stap en is volop in ontwikkeling. Denk bijvoorbeeld aan van koud naar warm tot frictie wassen.
Productieproblemen door verontreinigd recyclaat
Ondanks dit scheidings- en wasproces, blijft er regelmatig vuil in het recyclaat achter. Op het oog is dit niet waarneembaar. Maar als je verontreinigd recyclaat gebruikt, dan kun je in productie of tijdens de productlevensduur tegen allerlei problemen aanlopen. Denk aan een verminderde sterkte van het product, doordat de vervuiling lokaal voor een zwakke plek zorgt.Op de afbeelding hiernaast is bijvoorbeeld een breuk ontstaan door aanwezigheid van PET-vervuiling in een Polypropyleen product. Maar ook aan verkleefde en verstopte matrijzen. Daarnaast kun je oneffenheden of verkleuringen in je product ontdekken.
Het is dus erg belangrijk om van tevoren te weten of het recyclaat dat je gekocht hebt verontreinigd is. Misschien ervaar je al problemen en vraag je je af waar dit door komt. Ook in dat geval is een analyse van het recyclaat een goede stap om te ontdekken of de oorzaak bij verontreiniging ligt.
Soorten verontreiniging van gerecycled kunststof
Er zijn verschillende methodes om recyclaat te analyseren op verontreiniging. Deze leggen we hieronder uit. Welke analysemethode je het beste toe kunt passen hangt af van het type verontreiniging dat je verwacht aan te treffen. Er zijn drie soorten:
- Polymeerverontreiniging: denk aan Polyethyleen (PE) vervuild met kleine hoeveelheden Polyproplyleen(PP), afkomstig uit doppen, sluitingen of andere producten. Er kunnen bijvoorbeeld ook nog inkten en lijmresten in het recyclaat aanwezig zijn.
- Verontreiniging door vocht en vluchtige organische stoffen (VOC).
- Anorganische verontreiniging, zoals zand, klei, stof, metaal en vulstoffen.
Polymeerverontreiniging onderzoeken
Heb je het vermoeden dat er sprake is van polymeerverontreiniging? Dan kun je de DSC– (op basis van verhitting/koeling) en/of de FTIR-analyse (op basis van Infrarood) toepassen. Met FTIR-analyses worden met behulp van een infraroodscanner specifieke functionele groepen achterhaald – door middel van een uniek piekenpatroon – om het materiaaltype te identificeren. De focus ligt bij deze analyse op de verbindingen tussen de moleculen.
Bij sommige polymeren, zit er overlap in het piekenpatroon en is het met FTIR-analyse lastig te zien welke polymeren verontreinigd zijn. Dan kun je de meting aanvullen met een DSC-analyse. Bij DSC wordt er onder andere gekeken naar de smelttemperatuur, kristallisatietemperatuur en de Glas Transitie Temperatuur (Tg). Deze testmethode kan ingezet worden om het (hoofd) materiaaltype te identificeren, maar ook de verontreiniging van andere polymeren aan de hand van hun Tg of smelt punt te detecteren.
Tip: om een volledig beeld van polymeerverontreiniging te krijgen raden wij aan om beide analyses uit te voeren.
Verontreiniging door anorganische stoffen, vocht, VOC’s en vulstoffen uitsluiten
Vermoed je dat er vocht en anorganische stoffen in het materiaal zitten? Of dat er VOC’s vrijgekomen zijn tijdens het productieproces? Dan kun je dit op twee manieren achterhalen.
- TGA-test
Je kunt een sample thermografisch (laten) analyseren, afgekort TGA. Bij deze meting wordt het recyclaat verhit tot 800 °C. Tijdens dit verhittingsproces wordt de gewichtsafname gemeten. Zo kan er worden bepaald of er vocht of VOC’s vrijkomen en bij welke temperatuur de kunststof sterk in gewicht afneemt en dus degradeert. In de asrest van deze test vind je de anorganische stoffen terug. Hierbij kun je denken aan glasvezels, zand en vulststoffen zoals krijt en mineralen. - Verassingstest
Als je alleen de asrest wilt bepalen kun je ook een (simpelere) verassingstest uitvoeren. Bij deze test verhit je een sample tot 600 °C en meet je het gewicht voor en na de verassing.
Verbredende analyse
Wil je de asrest (de anorganische verontreiniging) uit de TGA of de verassingstest nog verder analyseren? Dan kan dat met behulp van een optische microscoop. Hiermee ontdek je hoe groot en welke vorm de deeltjes hebben. Zo kun je veel te weten komen over de bron van de verontreiniging.

Microscopische foto vervuiling in dunwandig product, gemaakt van recyclaat
Gespecialiseerde analyses voor extra verdieping
Om nog beter te bepalen met welke verontreiniging je te maken hebt, kun je een geavanceerde SEM-EDX microscoop inzetten. Hiermee bepaal je uit welke atomen de verontreiniging bestaat. Denk bijvoorbeeld aan aluminium of calcium door verschillende vulstoffen.
Als je met de TGA-analyse een hoge concentratie van VOC’s hebt waargenomen, dan kun je met behulp van chromatografie (GC/MS) analyseren welke dit zijn. Er zijn zelfs methodes die het gebruik van bijvoorbeeld UV-absorbers of andere additieven in hele lage concentraties in kunststoffen kunnen detecteren. Daarnaast kun je ook in de praktijk verontreiniging testen. Bijvoorbeeld door het filter residu (een stof die overblijft na een proces) na je extrusie verder te analyseren. Deze gespecialiseerde methodes gebruik je alleen wanneer het nodig is om de diepte in te gaan.
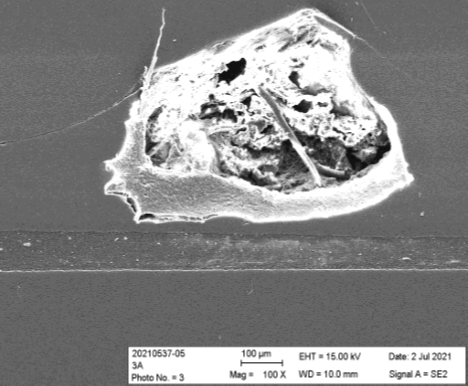
SEM-EDX zoom van dezelfde vervuiling in dunwandig product, gemaakt van recyclaat. Met SEM EDX is de samenstelling van deze vervuiling bepaald en kon de bron worden achterhaald.
Plan van aanpak
Verontreinigd recyclaat kan dus tot problemen leiden. Wil je dit oplossen of wil je meer weten dan alleen de specificaties van de leverancier? Dan stellen we onderstaand plan van aanpak voor:
.
Analyses gesubsidieerd (laten) uitvoeren
Om het gebruik van recyclaat te stimuleren, heeft het Ministerie van Infrastructuur en Waterstaat de ‘Tijdelijke subsidieregeling omschakeling naar verwerking circulaire plastics’ ter beschikking gesteld. Met deze subsidie krijg je 75% van de onderzoekskosten vergoed voor het uit (laten) voeren van productietesten en verbonden activiteiten, waaronder het selecteren en analyseren van het beoogde recyclaat. Er is per bedrijf tot € 25.000,- subsidie beschikbaar! De aanvraag is op 18 juni jl. geopend en loopt tot 3 oktober 2024. Op is op, dus stuur nog snel jouw aanvraag in. Lees meer over deze subsidie.
Hulp nodig?
We denken graag met je mee over welk type verontreiniging er zou kunnen spelen en welke test- en analysemethode daar het beste bij aansluit. Naar wens kunnen we je ook bij het uitvoeren van de analyses en productietests ondersteunen. Neem daarvoor vrijblijvend contact met ons op.
In onze vorige blog gaven wij u 3 manieren om te starten met een ‘groener’ plastic product portfolio, namelijk:
1) Gebruik maken van gerecycled plastic – oftewel recyclaat
2) Gebruik maken van biogebaseerde kunststoffen
3) Gebruik maken van bioafbreekbare kunststoffen
Voor deze onderwerpen geldt dat er uitdagingen en kansen liggen. In deze blog vertellen wij u meer over het gebruik van gerecyclede plastics.
Goodbye virgin, hello recyclaat!
Er zijn een aantal redenen waarom bedrijven gerecycled plastic willen gebruiken. De belangrijkste zijn milieuwinst en prijs. Gerecycled kunststof kost minder energie om geproduceerd te worden en door ze her te gebruiken, voorkomen we dat ze in het milieu terecht komen. Dit bespaart CO₂ en extra kosten! De kosten van recyclaat zijn momenteel lager dan die van nieuw (virgin) materiaal.
Daarnaast zien we dat consumenten, bedrijven en (semi) overheden steeds vaker duurzaamheid meewegen in hun aankoop. Onderscheidend vermogen door middel van inzet van recyclaat is dus gewoon onderdeel van het businessmodel vandaag; survival of the fittest!
Als laatste spelen overheid ambities en voortvloeiende regelgeving ook een rol. We hebben in Nederland afgesproken dat in 2030, 50% van de grondstoffen circulair moet zijn. Om hieraan te voldoen, kan de overstap naar gerecycled kunststof een belangrijke stap zijn. We zien nu al in Frankrijk dat het verplicht is om 20% circulaire content te hebben in alle overheidsaanbestedingen.
Dat recyclaat als alternatief voor virgin plastic kan worden ingezet, is in een breed scala aan producten al aangetoond. Denk hierbij aan verfemmers, zeepflessen, maar ook producten in de bouw zoals profielen, buizen en kappen.
Kortom; de weg ligt behoorlijk open met kansen om gerecycled plastic in te zetten. Toch zijn er een aantal overwegingen en voorbereidingen nodig.
Ja ik wil recyclaat inzetten, hoe nu verder?
De uitdagingen in het gebruik van recyclaat zijn te categoriseren in 3 onderwerpen.
- Beschikbaarheid
- Wetgeving
- Materiaaleigenschappen
Beschikbaarheid
Stabiliteit in kwaliteit en beschikbaarheid van het juiste materiaal is belangrijk voor een stabiel proces en eindproduct. De beschikbaarheid van kunststof hangt samen met de inzameling en sortering van het plastic. Er kan worden gesorteerd op type kunststof, product en/of kleur. Hoe beter het materiaal gesorteerd wordt, hoe beter de eigenschappen zijn. Dit proces is zowel kostbaar als technisch uitdagend. Neem bijvoorbeeld een handvat van een boormachine, deze bestaat uit twee types kunststof die aan elkaar vast zitten. Design-For-Recycling (denk aan modulariteit en ontwerp van monomateriaal) hangt daarom zeer sterk samen met de kwaliteit en beschikbaarheid van het recyclaat.
Wetgeving
De huidige wetgeving stimuleert het gebruik van gerecycled plastic. Normen worden langzaam maar zeker herschreven om gebruik van recyclaat niet te verhinderen. Toch zijn er een aantal kunststof toepassingen waarbij dit lastig ligt. De voedselwetgeving schrijft voort dat er in voedseltoepassingen buiten PET nog geen gerecycled kunststof mogen worden toegepast. Dit komt doordat contaminaties de voedselveiligheid niet gegarandeerd kan worden. Een verdieping van wat mag in uw segment wordt sterk aanbevolen.
Materiaaleigenschappen
Materiaaleigenschappen worden bepaald door recyclaat goed te sorteren (puurheid), wassen (verwijderen vervuiling, contaminaties, geur) en upgraden waar nodig. De materiaaleigenschappen van recyclaat zijn anders dan virgin kunststoffen. Belangrijk is om de relevante eigenschappen te weten van de virgin kunststof en een benchmark uit te voeren met het gerecyclede equivalent. Daarnaast kunnen de eigenschappen worden verbeterd door het gebruik van additieven tijdens de compounding stap of een verbeterde sortering.
Van uitdagingen naar innovatie
De Kunststof branche is zich goed bewust van bovenstaande mogelijkheden en uitdagingen. Bij de ontwikkeling van nieuwe producten wordt rekening gehouden met het gebruik van recyclaat, al dan niet van eigen retour stromen of vanuit ingezameld afval. In geval van retourstroom pilots wordt er veel geleerd over hoe producten terugkomen en weer worden ingezet als waardevolle grondstoffen Deze recyclaat stromen worden vaak opgewaardeerd om aan producteigenschappen te voldoen.
Wat opvalt is dat in alle kunststof segmenten vooral grote stappen wordt gezet door de ‘leaders of the industry’. Zij omarmen het nieuwe businessmodel dat rekening houdt met zowel een lage footprint, volledige recycleerbaarheid en prachtige product performances. Zie bijvoorbeeld het ELYSIUM matras van Auping wat bestaat uit een (mono) type kunststof en via retour systemen aan het einde van zijn levensduur weer terugkomt.
Bent u de volgende ‘leader of the industry’ en heeft u ambities om van start te gaan met recyclaat in uw product? Loopt u daarin tegen één van deze of andere uitdagingen aan? Wij pakken de uitdagingen graag met u aan. Onze materiaal- en verwerkingsdeskundigen van Polymer Science park helpen u verder met kennis, test- en prototype faciliteiten en een prachtig netwerk. Neem daarvoor vrijblijvend contact op.
Martine Bonnema, 16 mei 2023
De vraag naar kwalitatief goede grondstoffen blijft hoog, maar het aanbod wordt steeds beperkter. Goede ondersteuning in het navigeren door deze moeilijke markt is wenselijk, daarvoor kunt u terecht bij Keyser & Mackay.
Keyser & Mackay, een markgerichte agent en distributeur van chemische grondstoffen en industriële apparatuur, heeft zich aangesloten als deelnemer van Polymer Science Park. Ze hebben als bedrijf een sterke focus op chemische specialiteiten voor de formulerende industrieën, en bedienen een breed scala aan industrieën zoals coatings, inkten, kleefstoffen, kitten, kunststoffen en bouw.
“Transparantie naar onze klanten en opdrachtgevers is één van de belangrijkste elementen die ons onderscheidt van andere distributeurs.”
Keyser & Mackay is een Europees bedrijf met 125 medewerkers verdeeld over het gehele werkgebied en voor Nederland een eigen logistiek centrum in Rhenen. Ze vertegenwoordigen meer dan 100 leveranciers in de verschillende industrieën. Met het brede portfolio van additieven voor diverse toepassingen, hopen ze PSP-projecten verder te helpen naar succes.
PSP en Keyser & Mackay hopen elkaars netwerk te versterken en daarmee de kunststofindustrie te verduurzamen. De eerste kennismaken tussen beide bedrijven is als prettig en vertrouwd ervaren, een sterke basis voor een waardevolle samenwerking.